How to Calculate Bend Radius: A Comprehensive Guide
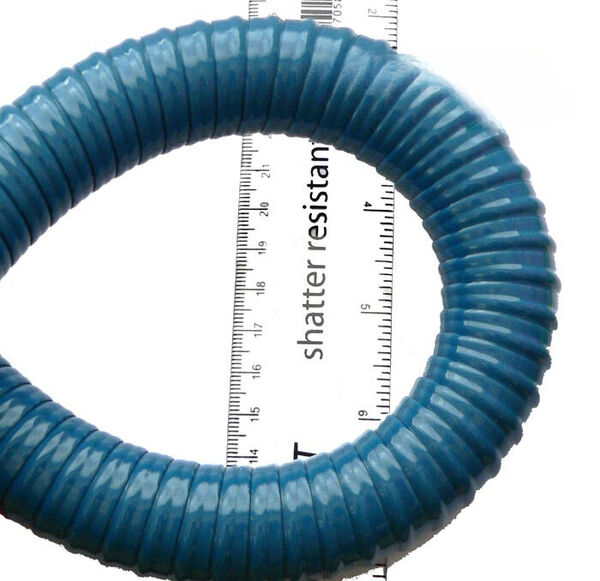
Knowing the calculation process behind the bend radius of hosepipes, ducting, and tubing is a crucial aspect for ensuring the free flow and efficiency of your transport systems, be it suction, delivery, or both.
You may be installing a new irrigation system, setting up a dust collection system in a workshop, or outfitting an industrial site with chemical transfer lines; understanding how to calculate the correct bend radius can save you from unfortunate expenses and headaches later on.
This guide will walk you through everything you need to know about the minimum bend radius for hoses, ducting, and tubing, why it’s important, how to calculate it for your specific needs, and the material impact on bend radius.
What is Bend Radius?
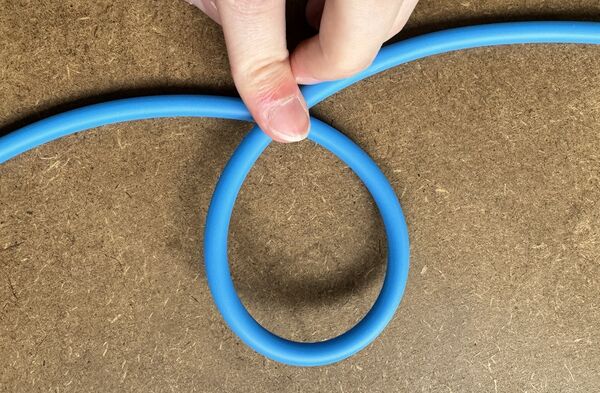
The definition of bend radius is: The minimum radius that a hosepipe, ducting, or tubing can be bent without damaging it or significantly reducing its lifespan. Bend radius is key in hose design and is the smallest radius that the hose can be bent without kinking, as kinking the hose would restrict whatever is flowing through it and potentially damage the integrity of the hose wall at the point of kinking.
- A smaller bend radius suggests greater flexibility.
- A larger bend radius indicates greater rigidity.
Understanding Bend Radius in Detail
Bend radius is a critical parameter that defines how tightly a hose, tube, or duct can be curved before it begins to kink, weaken, or even crack. This influences the design, application, and functionality of hose, duct, and tube systems across agriculture, engineering, all the way to aerospace. Selecting your hose based on bend radius plays a pivotal role in ensuring the integrity of your transfer systems.
The Science Behind Bend Radius
When hosing, tubing, or ducting is bent, the outer wall stretches and thins, while the inner wall compresses. This action introduces stress points that can lead to material fatigue, decreasing flow efficiency, and in severe cases, can cause complete system failure.
The bend radius and design specification ensure that the hose or ducting is operated within its material limits, preserving its structural integrity, operational capacity, and ensuring safe use.
Why Bend Radius Varies
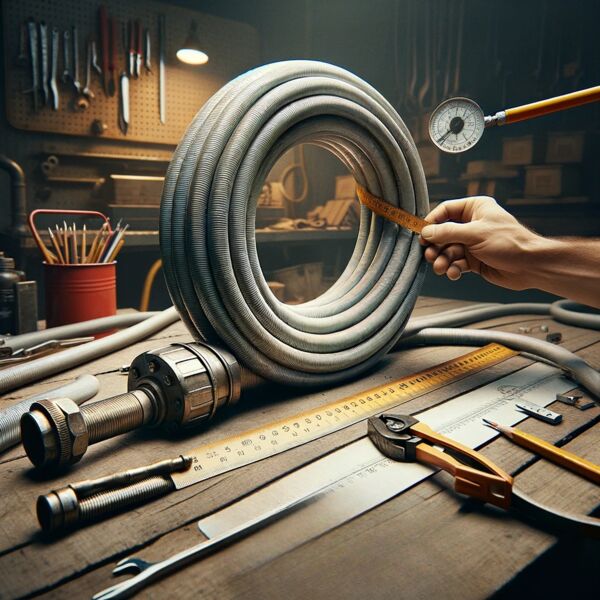
Different hose, tubing, and ducting products mean bend radius varies, largely due to material composition, construction techniques, and size. For instance:
- Material Flexibility: Soft, elastic materials like silicone tube or silicone hose offer a smaller bend radius in comparison to more rigid materials such as HDPE or galvanised steel.
- Reinforcement Type: In general, hoses reinforced with wire spirals, helixes, or rigid shells have a larger bend radius than those reinforced with textile braids.
- Wall Thickness: Thicker-walled hoses are generally less flexible, more durable, but require a larger bend radius to avoid damage.
Flexibility vs Durability: The Trade-off
Flexibility or durability? It’s a balancing act. A smaller bend radius generally offers more flexibility, enabling the hosepipe to fit into tight spaces and navigate around obstacles. However, increasing flexibility can often come at the cost of reduced durability (more flexible materials would need to be used that are not always as durable as their more rigid counterparts). On the other hand, a larger bend radius (generally a more sturdy or rigid hose) often comes with enhanced durability and resistance to external stresses but can limit ease of installation options due to its inflexibility or rigidity.
Why is Bend Radius Important?
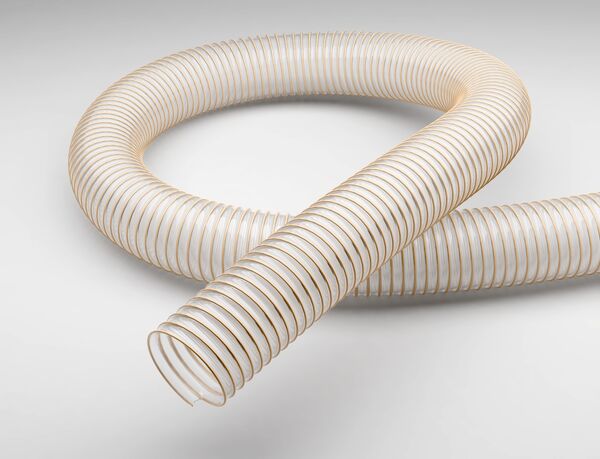
Ignore the bend radius? Bad idea. This can lead to several problems:
- Increased Wear and Tear: Bending a hose, tube, or duct beyond its bend radius can cause kinking, cracking, and other forms of damage, reducing its overall lifespan. From a safety aspect, this can be catastrophic.
- Reduced Flow: Excessive bending can reduce the flow through the hose, leading to inefficiencies and potentially system failures.
- Safety Hazard: In systems transferring hazardous materials, a compromised hose can pose significant safety risks. A hosepipe, once ruptured, can damage machinery, persons, or anything around it, especially if under high pressure.
How to Calculate Bend Radius
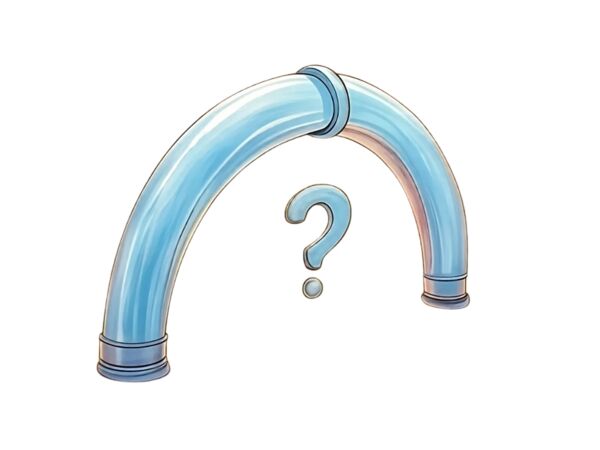
The calculation for bend radius is straightforward. It requires attention to detail to ensure accuracy. Here’s how to do it:
- Identify the Hose, Tube, or Ducting Type: Different materials and construction methods can affect flexibility. For example, a wire-reinforced hose will have a different bend radius than an unreinforced PVC tube.
- Consult Manufacturer Specification: Manufacturers usually provide a recommended bend radius for their products. This is often the safest, fastest route to finding out the bend radius.
- General Rule of Thumb: If manufacturer specifications are not available, a general guideline is that the minimum bend radius is approximately 4 times the internal diameter of the hose for hard hoses and 3 times for softer hoses.
For example:
For a hose, tube, or ducting with an internal diameter of 5 cm:
- Hard Hose: Minimum Bend Radius = 5 cm x 4 = 20 cm
- Soft Hose: Minimum Bend Radius = 5 cm x 3 = 15 cm
Engineering Calculation
In the absence of manufacturer data, engineers may use formulas that consider the following factors:
- Material Elasticity: The modulus of elasticity of the hose material can be used to estimate how it will deform under bending stress.
- Wall Thickness and Diameter: Thicker walls and larger diameters will typically reduce flexibility. An engineering approach may involve calculating stress on the hose wall upon bending and comparing this to the material’s yield stress.
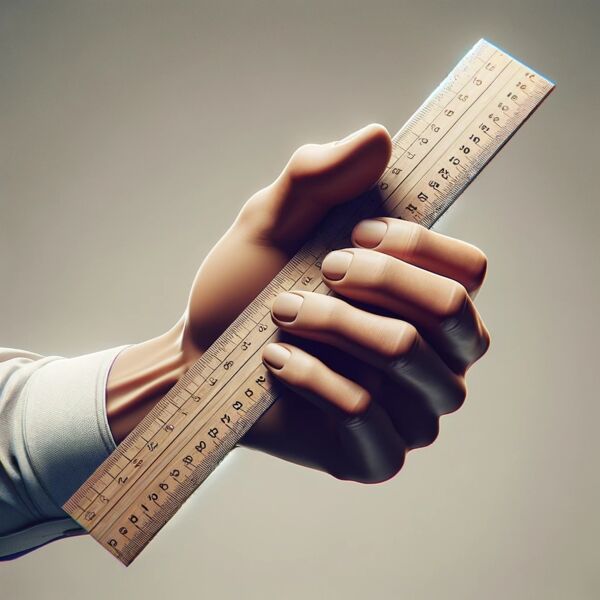
Empirical Testing
When more precise calculations are required, and there is no data to rely on, empirical testing can be performed:
- Gradually bend the hose, tube, or ducting while visually checking for signs of kinking, flattening, or other deformations.
- Now measure the radius, from the centre line of the hose, at the point just before these issues occur. This now becomes your minimum bend radius for that specific hose in these specific conditions.
Centre Line or Inner Edge?
Measuring bend radius from the hose's centerline, not the inner edge, offers a consistent reference. The centerline, as the neutral axis, stays stable during bending—unlike the compressing inner edge or stretching outer edge. This reflects the hose’s overall geometry, stress distribution, and performance, aligning with manufacturer specs and real-world use.
Working Within Bend Radius Limits
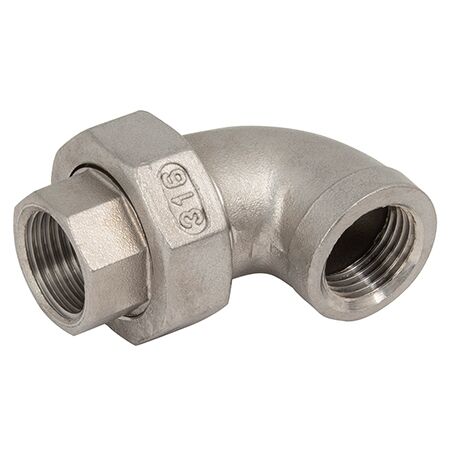
- Plan Your Layout: Before installation, plan the layout of your hose to avoid sharp bends and obstacles.
- Elbows and Fittings: If the system has sharp turns, incorporate elbows and other fittings designed to handle these angles without compromising or kinking the hose.
- Avoid Twisting: Twisting a hose along with bending it can reduce the bend radius and damage the hose.
- Regularly Inspect: Check your hose and ducting for signs of wear at bends and replace sections as necessary.
Conclusion
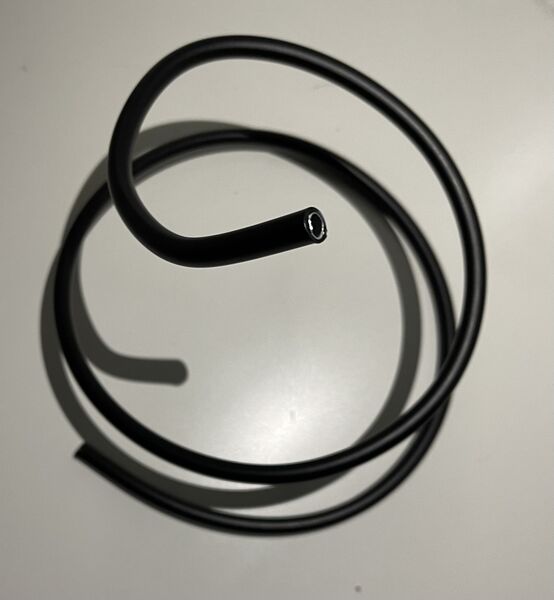
You must respect the bend radius in hosepipe, tubing, and ducting applications. It’s key to building an efficient and safe transfer system. By calculating and planning for bend radius ahead of time, you can avoid the common pitfalls that can lead to system failure or safety hazards.
Always consult with manufacturers and utilise their knowledge. Use high-quality fittings to ensure your system is up to the task, maintaining optimal performance. Remember, an efficiently planned and executed hose, tubing, conduit, or ducting system is an investment. This guide can also be used to measure the bend radius of conduit.
Manufacturer specifications are the most reliable source, but in their absence, a combination of understanding material properties, engineering principles, empirical testing, along with a suitable safety factor, can help determine the appropriate bend radius.
Frequently Asked Questions (FAQ) - How to Calculate Bend Radius
Q: What happens if I don’t know the internal diameter of my hose or ducting?
A: If the internal diameter isn’t known, measure it using a ruler or caliper at the hose’s opening. Alternatively, check any packaging or documentation that came with the product, as this information is often provided there.
Q: Can I use the same bend radius for all types of hoses or ducting?
A: No, bend radius depends on the specific material, construction, and intended use of the hose or ducting. Always check the manufacturer’s recommendations or apply the appropriate guideline (e.g., 3x or 4x the internal diameter) based on whether it’s a soft or hard hose.
Q: How do I know if my hose is ‘soft’ or ‘hard’?
A: A soft hose feels more pliable and bends easily by hand (e.g., silicone or thin PVC), while a hard hose is stiffer and resists bending (e.g., reinforced rubber or metal-lined hoses). If unsure, consult the product description or supplier.
Q: What should I do if my installation space is too tight for the minimum bend radius?
A: Consider using a more flexible hose material with a smaller bend radius, or incorporate fittings like elbows to manage tight turns without exceeding the hose’s limits.
Q: How often should I check my hoses for wear at bends?
A: Inspect hoses regularly based on usage—monthly for high-pressure or critical systems, and every few months for less demanding applications. Look for cracks, kinks, or flattening at bend points.
Q: Can temperature affect the bend radius of a hose?
A: Yes, extreme heat can make some materials more flexible (reducing the bend radius), while cold can make them stiffer (increasing it). Check the manufacturer’s temperature range for guidance.
Q: Is there a quick way to test bend radius without damaging the hose?
A: Yes, gently bend the hose in a controlled manner while watching for early signs of stress (e.g., slight flattening). Stop before kinking occurs and measure the radius at that point.
Q: What if the manufacturer’s specification seems too cautious?
A: Manufacturer specs include safety margins. If you think they’re overly conservative, consult an engineer to assess your specific application, but never exceed the recommended limits without expert advice.
Q: Can I calculate bend radius for non-circular hoses or ducts?
A: For non-circular shapes (e.g., rectangular ducting), bend radius calculations are more complex and typically require engineering software or empirical testing. Contact the manufacturer for guidance.
Q: How do I measure the bend radius after bending the hose?
A: Use a flexible measuring tape or a compass to trace the curve’s inner edge, then measure the radius from the centre point of the curve to the hose’s inner wall.
Get in Touch
Our team is ready to assist with enquiries, offer expert recommendations, and support your needs. Browse our blog, or get a quote to elevate your industrial capabilities.